Production Automation
Nowadays, when there is an emphasis on increasing production quality, labor productivity, and production flexibility, automation and robotics are the most suitable and efficient solution. Thanks to its continuous expansion, automation and robotics are becoming more accessible even for small and medium-sized businesses. Its implementation brings not only solutions to personnel issues and increased quality and productivity, but also financial savings in the short term.
Robotic Handling and Assembly
Because there is a vast number of applications, we divide the interface into the main machine and fixtures. Fixtures can perform numerous operations with different technologies, which is why they are separated in the modular robotics concept both in hardware and software. The main machine always includes several consistent components – a handling or motion unit (usually a robot or manipulator), input and output of material (typically conveyor systems), safety interface (fencing and electronic safety elements), and a user interface. We strive to standardize the machines to reduce acquisition costs and enable rental, testing, reconfiguration, etc. Fixtures will always be unique and require an individual solution.
Industrial Robot vs Collaborative Robot
Both systems have their advantages and disadvantages; it's not easy to say which is generally better or worse. For clarity, here are the basic characteristics for consideration:
Industrial Robot | Collaborative Robot |
---|---|
Faster and with a greater reach | The operator can enter the process (perform joint operation) |
Can handle heavy loads | Simpler setup and configuration – lower personnel qualification required |
Requires safety features, which increase application cost | Overall investment is lower |
More demanding programming and setup | Robot collaboration cannot be used for all technologies |
Financial Savings of Robotization
In our robotic cells, we implement industrial robots or 3-axis manipulators based on customer needs. We strive to simplify people's work and minimize the downsides of conventional single-purpose applications. That’s why we developed the modular machine system, which is the most efficient product for building machines on the market. This system, together with industrial robots, offers solutions for any production process.
Imagine needing to expand production, modify equipment, or change the production program. How complex would it be to reconfigure your current technology? With the modular machine system, it’s easy. You can adapt the modular system to current needs or market conditions, allowing you to respond to new requirements. This saves time and costs and ensures faster return on investment.
Subsidies for Robotization
From November 22, 2023, to February 15, 2024, applications are open for the Digital Enterprise – Technology 4.0 subsidy program, which allocates approximately CZK 1.5 billion for acquiring new technological equipment for automation, robotization, or optimization of business processes in line with Industry 4.0 principles in your business sector.
The subsidy covers up to 60% of costs (up to CZK 50 million). Projects must focus on the following areas within digital transformation:
● Production robotization – acquisition of machines, robots, lines, or additive technologies used in technological processes such as forming, machining, casting, assembly, etc. The goal is to acquire equipment that operates autonomously without requiring a human operator.
● Handling robotization – acquisition of systems like robotic arms, conveyors, or automated packaging machines with auto-wrapping, partially replacing manual labor.
● Storage robotization – implementation of intelligent storage systems such as chaotic robotic storage, automatic storage towers, tool dispensers, or automated transporters.
● Measuring and scanning technologies – acquisition of 3D scanners, quality control stations, or image analysis devices.
A condition for the subsidy is the integration of the production technology (e.g., CNC machines, welding/assembly robots, 3D printers, robotic arms, and software) with an existing or new information system. More info from our subsidy partner: www.dotacenamiru.cz
Modular Machine Building System
Machine Building Kit 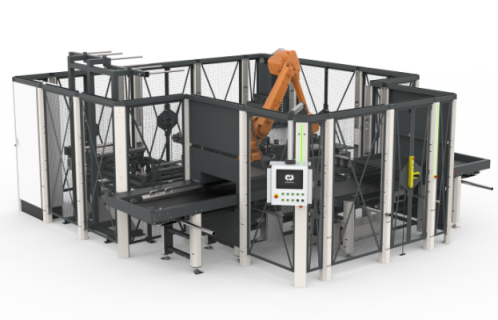
We simplify people's work and minimize the drawbacks of traditional single-purpose applications. That’s why we developed the modular machine system, the most efficient product for machine building on the market.
The modular system is a construction set where, using standard components or assemblies, we can jointly build complete machinery or automated lines tailored to your needs. This eliminates the disadvantages of conventional machines and gives you an easily accessible solution with simple deployment. More here: https://machinebuilding.cz/automatizace-a-robotizace/prumyslove-oploceni
Thanks to automatic exchange of entire technologies and modularity, fast deployment, expansion, and reconfiguration are ensured, along with easy replacement and compatibility – all with low cost and fast ROI.
Imagine needing to expand production, modify equipment, or change the production program. How complex would reconfiguration be? With the modular machine system, it’s simple. You can adjust it to your current needs or market demands, saving time and money and achieving a faster ROI.
Our modular system offers standard solutions like machine ECO and machine MRB, or customized solutions using machine PROFI. These machines are suitable for processing, automotive, aerospace, and other industries requiring automation and robotics.
The Most Efficient Machines Without Compromise
The modular machine system is currently the most flexible machine-building solution on the market. Its use eliminates common automation problems such as unmet expectations or cost overruns.
Thanks to high standardization and the ability to test in our application center, you are guaranteed on-time and on-budget delivery, functional results as expected, and achievement of original project goals. A key benefit is its clear design and execution.
The Modular System Is Simply...
Workshop and Training
We offer our customers a unique, comprehensive service through which we analyze your current processes and propose optimal automation and robotics solutions. This is a fully customized approach involving several process steps:
- We review your current production and identify key processes
- We study all materials related to the new product to optimize its production
- We analyze all processes and parameters in detail to maximize efficiency
- We identify suitable technology and production procedures to minimize downtime, storage, footprint, and scrap rates
- We present the ROI calculation for each optimized workstation